The tension of screen mesh is initially tensioned to a level that depends on factors such as mesh count. A 110 mesh with an 80 micron thread should be tensioned to 30 N/cm, while a 305 mesh with a 35 micron thread will reach only 16 N/cm. Regardless, both will lose tension dramatically and quickly. On average, we expect a tension loss of 25 percent within two hours, but the experience will be worse with the higher mesh counts.
The solution is simple. Re-tension the mesh and raise the tension to a level higher than the initial tension. A tension meter is not required. Each time you re-tension, you reduce the elasticity of the mesh. That is critical, because we do not want the mesh shifting laterally within the frame.
If the tension issue is not addressed, you can expect to spend extra time setting up a job, to wipe the bottom of screens between prints and to have colors out of registration. Productivity will be low, and prints will be heavy.
Looking exclusively at the productivity issue, a typical screen printer says he or she prints a one-color, dark ink on a light-colored shirt at a rate of 100-120 shirts per hour. When asked about white ink on a black shirt, the same person reports 35 shirts per hour. So how do we get the higher production when printing white ink on a black shirt?
First, the mesh must be at a tension level that can only be achieved by the re-tensioning process. High tension, along with the recommended printing technique, allows ink to shear better and to sit on the shirt’s surface without being driven into the garment. Ink printed through low-tension screens is also splattered on the garment rather than being placed with precision. Further, printing white ink on black also requires more-than-high screen tension. The opacity of a white dot placed on a black shirt depends on the construction of the dot. The dot must be sufficiently thick enough that the color of the shirt is blocked by the ink. Mesh that moves laterally within the frame smears—and therefore thins out—the dot.
Read the full article at Printwear Magazine.
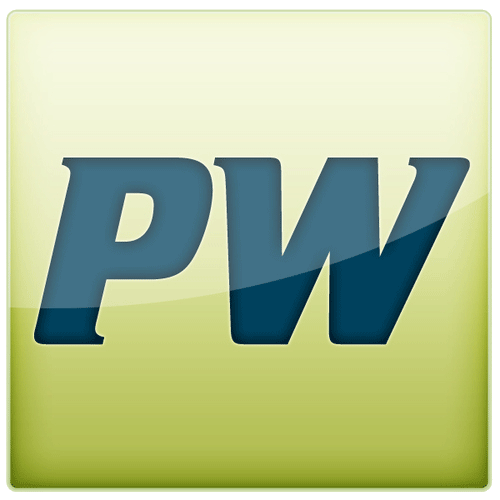
About the Author
- Email Address roger@rjennings.com