Every screen printing shop tries to run efficiently, but sometimes we get bogged down by the minutiae of day-to-day operations. So it’s important to set aside some time to analyze the systems in your screen printing department to make sure things are running smoothly.
If they’re not, here are three things you can do to improve efficiency and productivity:
Use Job Carts
Organize all your jobs on rolling carts. You can buy suitable rolling carts from your local industrial supply company or come up with your own design. The cart should be able to accommodate everything you need to set up and run a job. Those include:
- Garments
- Screens taped up, blocked out, and ready to go
- Inks, mixed and color-matched beforehand
- Squeegees and floodbars
- Ink knives
- Test garments or fabric pieces for initial startup
- An informative job ticket showing image placement and print order—and a color photo of the design
Pre-stage the carts, and when you are ready to start production roll the cart up to the press and set the job up as quickly as possible. When the print run is finished, tear down the job, putting the screens, squeegees, floodbar, ink, ink knives, and everything else back on the cart. Someone other than the press crew should then take that cart away and get things cleaned up while the next job cart is rolled up to the press and the startup procedure begins again. Make sure jobs are staged in advance so there is always another job ready to go. The only time you are making money is when your press is spinning, so by organizing your projects ahead of time you will reduce the time it takes to set up and turn jobs, increasing the number of projects completed and garments produced, increasing your profits. Imagine how your profit margin would improve by turning an extra job or two every day.
Get a Preregistration system—and USE IT!
It is easy to justify a preregistration system like M&R’s Tri-Loc to business owners, but you would be surprised by how many shops make the small investment, but don’t use it. That’s a shame because Tri-Loc allows an inexperienced worker to set up complex jobs in minutes. So don’t let your employees tell you they can do it faster without it. They can’t. The Tri-Loc preregistration system does more than help your setup crew quickly register the job from color to color. It also places the design on the garment in the proper position. Tri-Loc can easily cut your setup times in half, and with the introduction of M&R’s i-Image computer-to-screen (CTS) imaging and imaging/exposure technology, screen sets come out automatically preregistered, eliminating some of the human error that can frustrate setup crews. And the chance for human error is further reduced with M&R’s new Tri-Sync System™ and Tri-Sync Pallet™ (U.S. patent pending). On both i-Image CTS machines and on presses, Tri-Sync uses LEDs to let operators know when a screen frame has been properly secured against three electronically-linked stop points, virtually eliminating improper screen alignment caused by operator error.
Don’t be held hostage by your employees. Insist that they use Tri-Loc.
Maintain a Clean and Efficient Shop
Everyone knows that plastisol ink does not dry. You can leave it out forever and it will still wipe off on anything that happens to pass by. So it is vitally important that you wipe up ink drops and spills immediately. Ink on the floor will inevitably make its way into the office, your car, and then your home. Ink dropped on your press will end up on your hands, your clothes, and then on an expensive garment. If you want to reduce the time spent blowing out ink stains, make sure your employees clean up after themselves. Sometimes the simplest idea ends up saving you a lot of money. This just may be the one.
Related Products
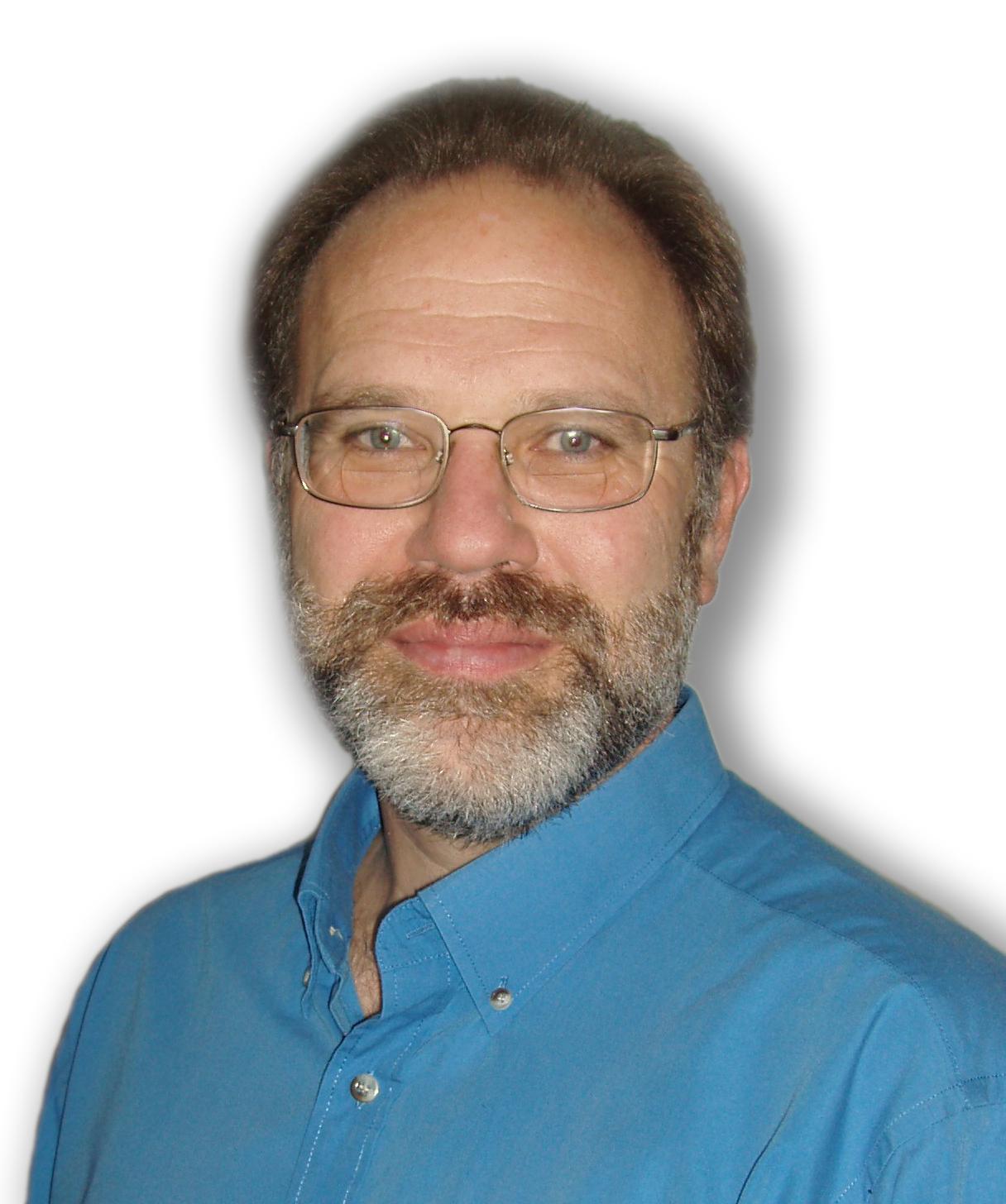
About the Author
- Email Address glen.carliss@mrprint.com
- Phone +1 630 258 1194